Laser Welders: A comprehensive guide to laser welding technology
Laser welders are advanced devices that use laser technology to join materials such as metals and plastics. They have gained popularity in recent years due to their precision, speed and applicability in various industries. In this article, we will take a closer look at this innovative technology, discussing its operating principles, advantages and disadvantages, different types of laser welders and practical applications.
Introduction to laser welding machine
A laser welder is an advanced device that uses laser technology to join various materials, such as metals and plastics. In industry, laser welders are gaining popularity due to their precision, speed and applicability in various industries. In the following sections, we will discuss the principle of equipment using laser technology, the components of a laser welder, and the differences between a laser welder and traditional welding methods.
Operating principle of the device using laser technology
A device using laser technology works by concentrating a beam of laser light on the materials to be joined, which leads to their fusion and fusion. The principle of the laser welder is to generate a laser beam through a laser source, which is then directed to the surface of the material to be welded by means of an optical system. As a result of this process, the material is melted, and when it cools down, it forms a permanent connection.
Laser welding machine components: from laser source to welding head
Components of a laser welding machine include the laser source, the optical system and the welding head, among others. The raycus laser source is one of the popular manufacturers of laser sources that generate a laser beam with the appropriate power and wavelength. The optical system consists of mirrors and lenses that direct and focus the laser beam on the materials to be joined. The welding head is the component that directly contacts the material and guides the welding process, providing the right conditions for the formation of a permanent joint.
Differences between laser welding machine and traditional welding methods
Compared to traditional welding methods, such as arc or gas welding, laser welding offers a number of advantages. First of all, laser welding is characterized by greater precision, which makes it possible to join even very thin and delicate materials. In addition, the laser welder allows faster welding, which translates into higher productivity. It is also worth noting that laser welding generates less pollution and harmful gases, which contributes to better protection of the environment and the health of workers.
Advantages and disadvantages of laser welding
Main advantages of laser welding: from quality to speed
The main advantages of laser welding include high quality laser welding, high welding speed and precision. Laser welding makes it possible to achieve very clean and durable joints, which translates into better strength and extended life of welded parts. As a result, laser welding is especially recommended for joining materials with high quality requirements, such as aerospace or medical components.
Disadvantages of laser welding: from cost to technical limitations
Although laser welding has many advantages, there are also some disadvantages to laser welding. One is the high capital costs associated with purchasing and maintaining laser welders. These devices tend to be more expensive than traditional welders, which can be a barrier for smaller companies.
Another disadvantage of laser welding is technical limitations, such as lower penetration depth compared to some arc welding methods. As a result, laser welding may not be suitable for joining very thick materials. In addition, laser welding requires precise parameter settings, such as laser power and wavelength, which can be difficult for some operators.
In summary, the advantages of laser welding include high quality, high welding speed and precision, while the disadvantages of laser welding include high costs and technical limitations. Choosing the right welding method depends on individual needs and requirements, and laser welding can be an excellent solution for joining materials with high quality requirements and in situations where speed and precision are crucial.
Different types of laser welding machines
There are various laser welding machines on the market, which differ in their specifications and applications.
The speed of laser welding is much higher than that of traditional welding methods, resulting in greater productivity and time savings. In addition, laser welding allows the joining of various materials, such as metals, plastics and ceramics, which increases the range of applications for this technology.
WELDFOX 1500W 3W1 laser welder, 2000W and 3000W: comparison of popular models
There are various models of laser welders on the market, including a 1500W laser welder, a 2000Wlaser welder , and a 3000Wlaser welder . Each of these models has its own unique features and specifications, which are worth comparing before choosing the right laser welder.
When comparing these three models of laser welders, it is worth noting the laser power, wavelength range and depth of penetration. Choosing the right laser welder depends on individual needs and requirements, and comparing the specifications of each model can help you make the right decision.
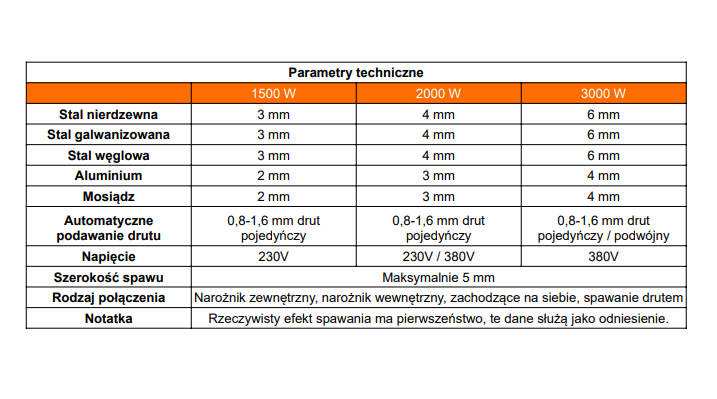
Applications of laser welding
Laser welding is a material joining technique that is used in many different industries. In this section, we will discuss laser welding applications in welding metals, including stainless steel, and other laser welding applications in various industries.
Welding of metals: stainless steel and other materials
Metal welding is one of the main applications of laser welding. Due to its precision and ability to reach high temperatures, laser welding is particularly effective for joining metals such as stainless steel, aluminum, copper and titanium. Stainless steel is a difficult material to weld using traditional methods due to its corrosion resistance and high strength. Laser welding produces clean and durable joints, resulting in better strength and extended life of welded parts.
In the case of stainless steel welding, laser welding minimizes the effect of heat on the material, which reduces the risk of deformation and loss of corrosion-resistant properties. In addition, laser welding is also used to join different types of metals, which is difficult or impossible to achieve with traditional welding methods.
Laser welding applications in various industries
The applications of laser welding are wide-ranging and cover various industries. Here are some examples of laser welding applications in various sectors:
- Automotive industry: laser welding is used to join car body components, exhaust systems, and in the manufacture of batteries for electric vehicles.
- Aerospace: In this industry, laser welding allows the joining of aircraft structural components, aircraft engines and other components with high quality requirements.
- Medical industry: Laser welding is used in the manufacture of implants, surgical instruments and other precision components used in medicine.
- Electronics industry: In this industry, laser welding allows the joining of thin-film materials and microelectronic components, such as integrated circuits and electronic connectors.
- Energy industry: laser welding is used in the manufacture of components for wind turbines, solar panels and other energy system components.
In summary, laser welding applications are wide-ranging and cover a variety of industries where precision, strength and high quality joints are required. Laser welding is particularly effective for welding metals such as stainless steel, resulting in better strength and extended life of welded parts.
Practical aspects of using a laser welding machine
In this section, we will discuss the practical aspects of using a laser welding machine, including technical settings, maintenance, and the cooling system and shielding gases.
Technical parameters and settings: laser source power, wavelength and penetration depth
The technical parameters of a laser welding machine are crucial to the quality and efficiency of the welding process. The three main parameters to pay attention to are the power of the laser source, the laser wavelength and the depth of penetration.
The power of the laser source affects the speed and quality of welding. Higher power allows for faster welding and a better combination of materials, but it can also cause a higher risk of deformation. Therefore, it is important to choose the right laser power for the type of material and thickness of the parts to be welded.
The wavelength of the laser determines the laser’s ability to penetrate the material. The wavelength affects the absorption of energy by the material, which directly affects the quality of the weld. The wavelength of the laser should be selected according to the type of material to be welded.
Penetration depth is the distance the laser energy penetrates the material. The depth of penetration depends on the laser power, wavelength and material properties. For optimal results, the penetration depth should be adjusted according to the thickness of the material and the type of joint.
Cooling system and shielding gases: how to take care of a laser welder
The cooling system is an indispensable component of a laser welder, which ensures the proper operating temperature of the device. The cooling system can be water-based or air-based, depending on the model of the welder. It is important to regularly check the condition of the cooling system, clean the filters and refill the coolant to ensure the long life of the laser welder.
Shielding gases are used in laser welding to protect the weld surface from chemical reactions with the environment. Shielding gases, such as argon or helium, form a protective layer around the weld, preventing oxidation and other adverse reactions. Regular checking and refilling of shielding gas is key to maintaining high weld quality and long-term use of the laser welder.
In summary, the practical aspects of using a laser welder include both proper settings of technical parameters such as laser source power, laser wavelength and penetration depth, as well as taking care of the cooling system and the use of shielding gases. Regular maintenance and inspection of these components will ensure the long life of the laser welder and high quality welds.
The future of laser welding
In this section, we take a look at the future of laser welding, discussing potential innovations and developments in the technology. Laser welding has tremendous potential to influence Industry 4.0 and contribute to the further development of various industries.
Innovation and development of laser welding technology
Laser welding technology is constantly evolving, resulting in better performance, higher quality welds and greater process efficiency. Among the potential innovations that could affect the future of laser welding are:
- New laser sources with higher power and better energy efficiency, which will allow faster and more precise welding.
- Improved cooling systems to better protect equipment from overheating and extend its life.
- Intelligent control systems that automatically adjust welding parameters to the type of material and the requirements of a specific application.
- Integrating laser welding with other technologies such as 3D printing to create more complex and precise structures.
With the development of laser welding technology, it can be expected that it will become increasingly available for a variety of industries and applications, further increasing the popularity of this welding method.
The role of laser welding in Industry 4.0
Laser welding plays a key role in the context of Industry 4.0, which is characterized by automation, digitization and intelligent management of production processes. Introducing laser welding into Industry 4.0 can contribute to:
- Increase production efficiency with faster and more precise welding.
- Improved product quality, thanks to a better combination of materials and less risk of welding defects.
- Reduced production costs, thanks to lower energy and material consumption and longer life of welding equipment.
- Collaborate with other technologies, such as 3D printing, to create more complex and precise designs.
As such, laser welding has great potential to influence Industry 4.0 and contribute to the further development of various industries. As the technology develops, laser welding can be expected to become more common and indispensable in industry.
Summary
In this article, we discussed laser welders and laser welding technology, outlining its operating principles, components, advantages and disadvantages, different types of welders and applications in various industries. We also discussed practical aspects of using a laser welder, such as technical parameters, settings, and cooling systems and shielding gases. Finally, we looked at the future of laser welding, discussing innovations, developments in the technology and its role in Industry 4.0.
In summary, laser welding is an advanced technology that offers many advantages, such as high quality welds, process speed and precision. At the same time, laser welding has its drawbacks, such as high investment costs and technical limitations. Nevertheless, as the technology continues to develop, laser welding can be expected to become increasingly common and indispensable in industry, influencing the development of various industries and contributing to the automation and digitization of manufacturing processes as part of Industry 4.0.